What is a cobot? - Read more about the welding robot
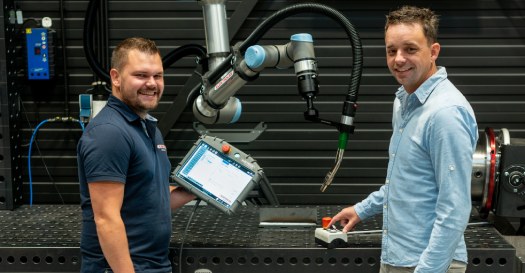
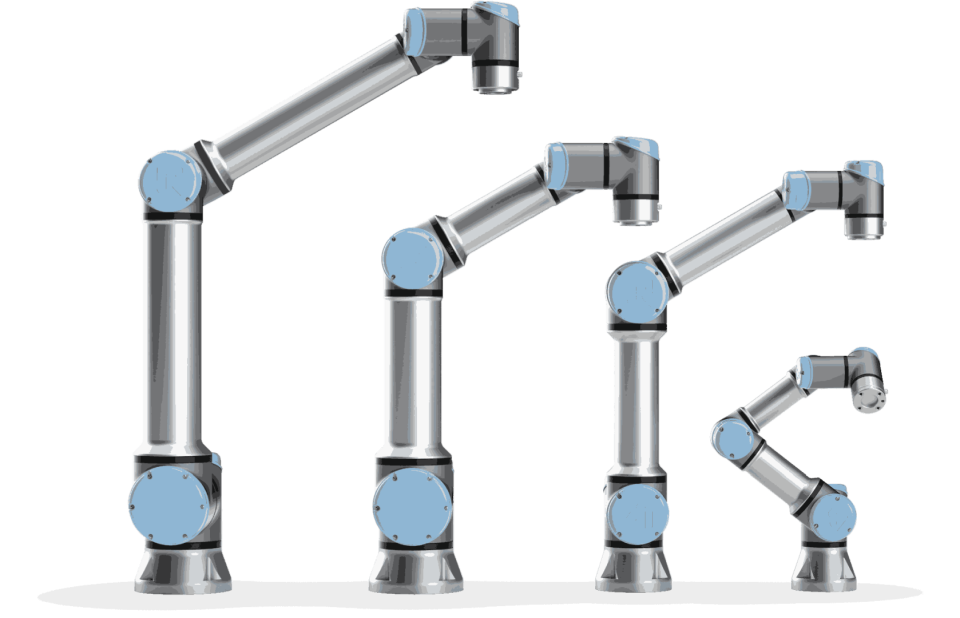
Benefits of a cobot
Cobots have become increasingly popular in welding applications because of their numerous advantages. Here are some reasons why you should consider using cobots in your welding process:
- Increased productivity: Cobots can work around the clock without getting tired or making mistakes.
- Improved quality: Cobots weld very precisely with consistent accuracy;
- Improved worker safety: Collaborative robots are designed to work safely with human workers;
- Flexibility: Cobots are easy to program, allowing them to complete tasks quickly;
- Cost-effectiveness: Cobots can perform welding tasks at a lower cost than traditional robots.
These cobot advantages are causing more and more companies to improve their welding process by using a cobot.
Cobot and industrial robotic
Cobot or a traditional robot are often taken apart. But what are the differences? Cobot is made to work alongside human workers. One of the main differences is that a cobot is made to work side by side with human workers.
The cobot: Collaboration with humans
Unlike a cobot, a traditional robot is used for repetitive work. Because of this, a robot must first be programmed. These robots perform tasks with great precision. Which makes it ideal for mass productions. To ensure welder safety, robots are separated from work areas. Whereas this is not necessary for a cobot setup.
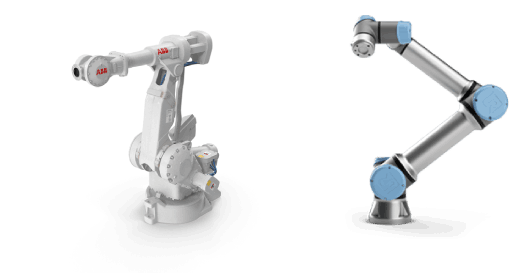
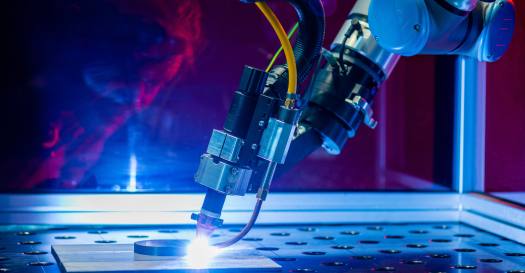
Tips: which processes you can use
Here are some of the collaborative welding techniques that can be implemented with cobots:
- MIG/MAG welding
MIG welding, or metal-inert gas welding, is a process in which electric arc is formed between a melting wire electrode. Cobots can perform MIG welding with high accuracy and repeatability.
Overall, cobots offer a wide range of benefits when it comes to welding. Implementing cobots in your manufacturing process increases productivity. In the process, it also improves welding quality and the safety of your workers.
Overall, cobots offer a wide range of benefits when it comes to welding. Implementing cobots in your manufacturing process increases productivity. In the process, it also improves welding quality and the safety of your workers.
- TIG welding
TIG welding or wolffram intergas welding is used to weld thin metal sheets or for welding non-ferrous metals. Cobots can perform TIG welding with great accuracy, making it an ideal technique for applications where precision is crucial.
- Spot welding
Spot welding uses electric current to fuse two metal pieces together at specific points. This technique is often used in the automotive industry and other applications where high-speed welding is required. Spot welding can also be realized using a cobot. With high accuracy and speed, the cobot is ideal for spot welding.
- Stud Welding
Stud welding is a welding process in which a metal pin or stud is permanently attached to another metal surface, usually a plate. This is done by heating the pin or stud and then forcefully pressing it against the other metal. The joint is created as the joining materials melt and fuse together, creating a strong and durable bond.
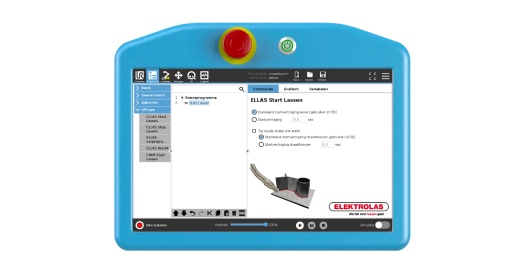
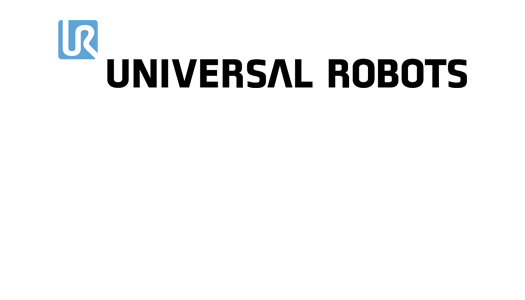
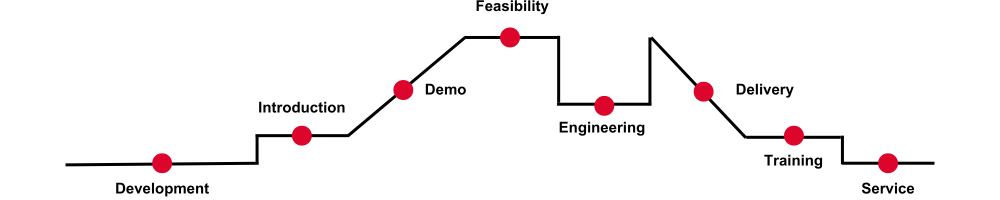
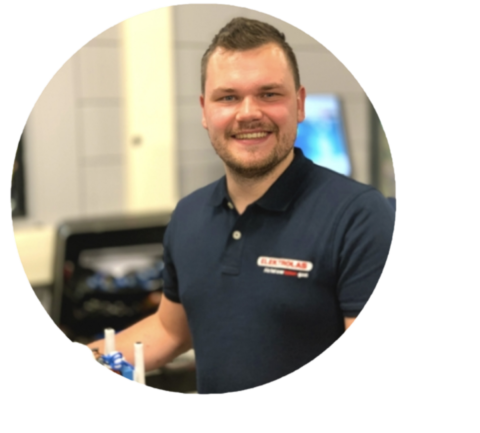
Our Overall Approach
When it comes to welding, Elektrolas has all the knowledge and resources in-house. We are a point of contact for all those involved in the welding process, from tendering to quality control. We are a total provider in the welding field. We secure quality, offer training, sell, rent and service on welding equipment. This is our disc-of-five. Five services that reinforce each other. That is how we ensure that our customers are ready for the future.
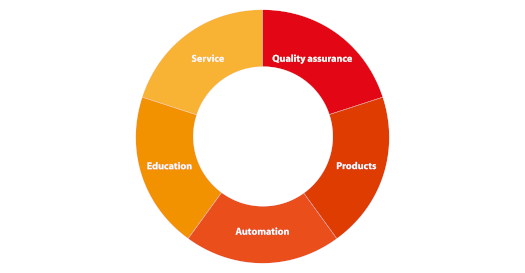