Jesse
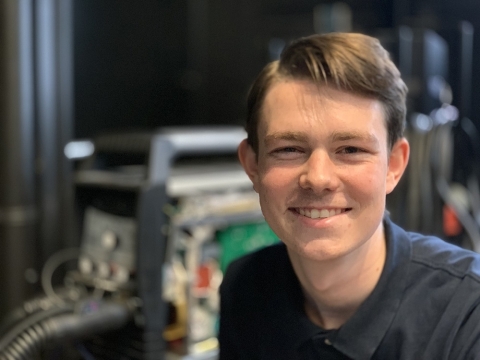
‘Through Our Welding Portal, our customers have insight
into the status of their machinery at any time.’
Jesse Cornelissen-Uijl
Service Engineer
T: +31 (0)416-336777
E: jesse@elektrolas.com
into the status of their machinery at any time.’
Jesse Cornelissen-Uijl
Service Engineer
T: +31 (0)416-336777
E: jesse@elektrolas.com
"Preventive maintenance prevents repairs"
Since August 2020, Jesse Cornelissen has been a Service Department employee at Elektrolas. He combines this with the BBL course MBO 4 Middle Management Engineering. That he ended up in engineering is the result of a search of several years. He talks thoughtfully, politely, confidently and with growing enthusiasm about his work, which takes place both in the workshop and with customers.
Work and school
‘How I ended up at Elektrolas is quite a story after all. I was 17 and should have done another year of Havo 4, but I decided to go to Sweden with my parents, who started a campsite there in the middle of the woods. While waiting for my emigration, I worked full-time for a while in the restaurant where I had a part-time job. The hospitality industry attracted me so much that I started at cookery school in Sweden. And although going abroad was a very special experience, it soon became clear to me that I was not going to be happy there. I decided to return after nine months, having applied for a Dutch cookery school, where I could enter in the second year of study. I started living with my girlfriend in my in-laws' house and finished the course. But eventually you start thinking about what you really want. Because engineering had always interested me, I looked into that direction and decided, after visiting a few open days, to combine work and school via the BBL course MBO 4 Middle Management Engineering. A teacher told me about Elektrolas.’
Pizza night
‘My job application was a great experience. The building of Elektrolas is beautiful and the workshop very well cared for. That says something about the way they work. The interview was about my motivation. The questions were well put and there was an immediate click. Coincidentally, on my first working day a pizza evening was organised for which I was invited, even though I had just joined the team. That evening, we talked about the future developments of the service department. Immediately into the deep end, then; it couldn't have started better. I now enjoy working as a service technician. I feel that I can develop very well here. I am also doing well at school. Elektrolas and this job came at exactly the right time in my life.’
Machinery
‘I work four days a week. When I am inside, I repair welding torches and welding machines. Part of my time is spent on the job, alone or with a colleague. We visit companies where there are sometimes 70 or 80 machines and take care of repairs, maintenance, inspections and validations. I have found that preventive maintenance prevents repairs. In workshops, metal dust can be disastrous and cause breakdowns. Not only because of short circuits, but also because it can clog up the cooling system. During a service, we therefore clean the inside of the machines and check the contacts and cables. Then they are connected to a diagnostic device for the electrical safety inspection. If, for instance, there is an earth leakage problem or if the resistance values of the welding circuit are not correct, this will come to light in no time. If a company has to comply with a certain certification, we will also validate the equipment. All observations and repairs and maintenance work are recorded in Our Welding Portal. This gives our customers insight into the status of their machinery at any time.’
Overall picture
‘At Elektrolas, I feel right at home. I have grown, in my technical skills and as a person. I also get on well with our customers. Up close, I see Elektrolas developing continuously. More customers, more rentals, more sales and therefore also work for the service department. Together with training and quality management, a total picture for our customers. Even after my training, I would like to remain part of this team.’
More info about Service
Our Overall Approach
When it comes to welding, elektrolas has all the knowledge and resources in-house. We are a point of contact for all those involved in the welding process, from tendering to quality control. We are a total provider in the welding field. We secure quality, offer training, sell, rent and service on welding equipment. This is our disc-of-five. Five services that reinforce each other. That is how we ensure that our customers are ready for the future.
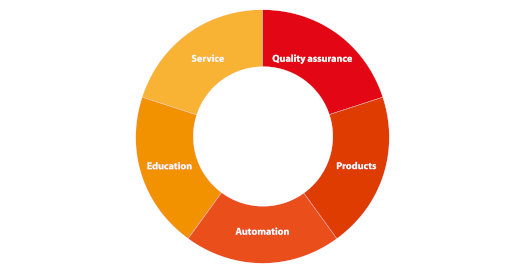