Thije
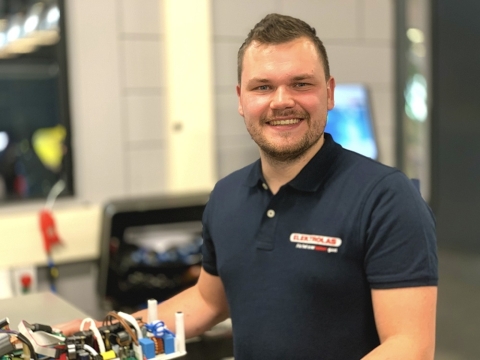
‘Our customers should experience low to
service and maintenance by Elektrolas.’
Thije van Delft
Industrial Autmotion & Product innovation
T: +31 (0)631901356
E: thije@elektrolas.com
service and maintenance by Elektrolas.’
Thije van Delft
Industrial Autmotion & Product innovation
T: +31 (0)631901356
E: thije@elektrolas.com
"Even seemingly impulsive decisions I never take unthinkingly"
Eager to learn, enterprising, customer-focused and a little headstrong. That is soon the conclusion after meeting Thije van Delft, engineering team leader at Elektrolas. ‘I started at Elektrolas as a mechanic in 2014, when I was looking for a new challenge. As the service team continued to grow, I was given the opportunity to become team leader in 2019. Together with my colleagues, I ensure continuity in our customers' machinery.’
Service
‘Elektrolas' service department provides repair and maintenance of all welding equipment. Because we have an extensive spare parts warehouse, we can serve our customers quickly. And should a repair take a little longer, we have replacement equipment available. Besides repairs and maintenance, our service team carries out safety inspections and verifications according to the applicable NEN standards. If new equipment is delivered, we take care of commissioning and adjustments to software and hardware. We clearly record the history of repairs, maintenance and inspections in Our Welding Portal.’
Training
Thije and engineering. ‘At home in Waalwijk, I was the only boy among three sisters. As a child, I helped my father restore old Peugeots and weld go-karts. It suits me to solve many things independently. This probably has to do with my hearing; I was born hearing impaired. That created a certain social isolation. I went to special education in Sint-Michielsgestel, so my social circle wasn't really around the corner either. Nevertheless, that education brought me a lot. This VMBO Technical School actually put me on the right track, so that after graduation I was able to move on to a regular ROC to study Constructional fitter. I then became a mechanic at a company specialising in hydraulic systems, until I was ready for the next step. I found this at Elektrolas and spent the first four years combining my mechanic job with studying MBO 4 Mechanical Engineering.’
Accessibility
‘At Elektrolas, I have plenty of challenge in my work. I enjoy developing - together with my colleagues - ideas that make our work better. Better for our customers, I mean. They must experience low-threshold service and maintenance by Elektrolas. I think responsibility in this is super, and I get that space here. An example: in 2019, I was given the opportunity to go on the road and redesign my company car. I got to work not only on the service van itself, but also on the work processes around it. Such as digital work orders, with which we were one of the first, and a stock system for the materials in our service vans, so that our mechanics never miss out again. That same year, the question came up whether I wanted to become team leader. The service team consists of a team of fine motivated colleagues, so that's what I wanted.’
Opportunities for improvement
‘Elektrolas' employer style leads to personal development. I am also not the type to constantly be on our service technicians' necks, because they have a lot of baggage and experience and follow periodic training and courses. What I have learned along the way is the way I communicate my proposals. How do I tackle improvement opportunities in my department? By weighing things up and coming up with appropriate structures. If I think something is a good solution, I look for the bears on the road. If there are none, I share the plan with the team. So even seemingly impulsive decisions I never take unthinkingly. We also share knowledge among ourselves. We sometimes jokingly say: if the sweat is on our backs and we can't solve a complicated problem, that's the moment to call on each other's help. That way, there is no situation our service team cannot tackle.’
Future
‘The customer of tomorrow is making more and more demands.On the shop floor, software is becoming increasingly important in controlling welding machines; these are in direct contact with the drawing office.The welding data management system records welding data.It records which welder worked on which project, when, with which machine and with which parameters.This ensures better traceability and more insight into quality and throughput times. To increase capacity, we are increasingly using cobots. These collaborative robots deliver consistent quality and can work with or alongside people.Cobots are smaller and lighter than industrial robots and have built-in safety features.They are easy to program and can be used for welding, grinding and gluing, but also for loading and unloading CNC milling machines.Within Elektrolas, further digitisation of inventory management is leading to new possibilities in the service area.We might even develop a kind of McDrive for maintenance and parts.How intensively we continue to grow, I obviously cannot predict, but in connection with a reasonable drive time it is practical if we can serve our service customers within a radius of about 50 kilometres. One thing is certain: Elektrolas will continue to work on continuity in the welding workshop of the future.’
More info on Service
More info on Automation
Our Overall Approach
When it comes to welding, elektrolas has all the knowledge and resources in-house. We are a point of contact for all those involved in the welding process, from tendering to quality control. We are a total provider in the welding field. We secure quality, offer training, sell, rent and service on welding equipment. This is our disc-of-five. Five services that reinforce each other. That is how we ensure that our customers are ready for the future.
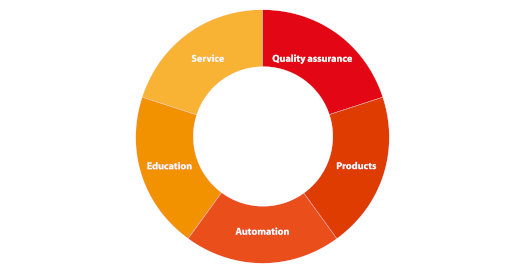