Thomas
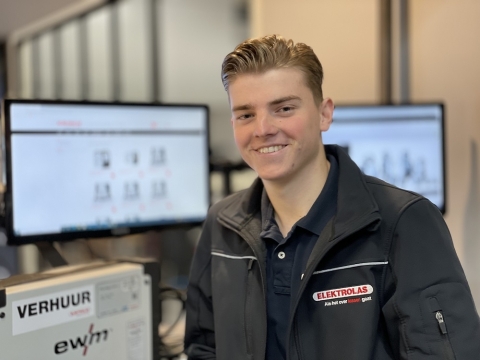
‘To give the right advice, you have to
be alert and sometimes creative.’
Thomas van Wanrooij
Coordinator Service Department
T: +31 (0)6-82404892
E: thomasvanwanrooij@elektrolas.com
be alert and sometimes creative.’
Thomas van Wanrooij
Coordinator Service Department
T: +31 (0)6-82404892
E: thomasvanwanrooij@elektrolas.com
To give the right advice, you have to be alert and sometimes creative
There can be many reasons why Elektrolas customers come to Waalwijk. At the entrance, they are welcomed and spoken to by counter employee Thomas van Wanrooij. Thomas joined Elektrolas in 2020 through a technical graduate internship. On the one hand, his preference lies in customer contact and on the other in engineering. Hence, he not only mans the counter, but also supports the service department with repairs and inspections. Part of the week, Thomas drives his regular route with orders and repaired machines.
Technical and commercial
‘The work I enjoy most is always at the interface between engineering and commercial. Before I started my mbo-4 Hightech Metalektro, I started the Junior Accountmanager course, i.e. sales. But it turned out that this course focused too much on economic subjects; they don't suit me as well. The great thing about my job as a desk clerk is the combination of tasks in front of and behind the scenes. I am busy with technology, but fortunately have a lot of customer contact. I like the variety between indoor and outdoor work. Customers come by for spare parts or consumables, for instance, or want to know more about the welding machine they have their eye on. I also take on repairs of welding machines, torches and electric hand tools, among other things. In the workshop of our service department, I carry out repairs, maintenance and inspections. I drive my delivery route on fixed parts of the week. Then I take stock of which of our customers' consumables need replenishing. I also deliver rental machines and return repaired goods.’
Point of contact
‘As a counter clerk, in many cases you are the first point of contact. I see it as an important task that everyone with a question or a repair knows where they stand. The standard turnaround time for incoming repairs is a week. Every job is neatly documented and entered into the system so that we can track progress and keep the customer informed. If someone comes in with a specific technical question, for example during the decision-making process around a new machine, I will bring in one of our specialists so we can make a proposal that matches the requirements. Elektrolas has a suitable answer for every need. Recently, someone came to the counter who wanted to do production welding without having access to power. We put together a configuration for him where he could use the normal 220-volt network. To give the right advice, you have to be alert and sometimes creative. Like recently during renovation work in a historic building. There, in the lift, a piece of sheet steel twelve millimetres thick was in the way. Recommending the right type of plasma cutter was only half the solution. The real problem lay in the fact that the space was too small to get a plasma jet going without further ado. We therefore ensured adequate safety provisions, such as an exhaust and fire blankets. Real customisation, in other words.’
Internal training
‘At Elektrolas, I get every opportunity to become better at my job, so I learn every day. For instance, I take internal training courses on welding. Every period, a different welding technique is discussed and I receive explanations about its application in combination with various applications and types of metal. I also get the opportunity to develop more in SolidWorks and the 3D printer. That is inventing and experimenting at the same time. So many interesting developments are taking place at Elektrolas that I don't quite know yet in which direction I want to develop further. And whether I will do another higher vocational education course in the field of sales or engineering, for example part-time. Take the cobot, for instance. Elektrolas started working on this early on, so that we now have a head start and can properly market this cooperative robot arm. Craftsmanship in welding workshops remains important, but the problem is the shortage of qualified employees. The cobot increases their productivity by pre-processing and positioning materials or performing serial welding production runs. Elektrolas' offer does not stop at supplying machines, of course. Training is also part of our Disk of Five. So meanwhile, the Elektrolas Welding School provides demos and training in programming and applying the cobot. One of many examples showing Elektrolas' vision of the welding workshop of tomorrow.’
More info on Service
More info on Products
Our Overall Approach
When it comes to welding, elektrolas has all the knowledge and resources in-house. We are a point of contact for all those involved in the welding process, from tendering to quality control. We are a total provider in the welding field. We secure quality, offer training, sell, rent and service on welding equipment. This is our disc-of-five. Five services that reinforce each other. That is how we ensure that our customers are ready for the future.
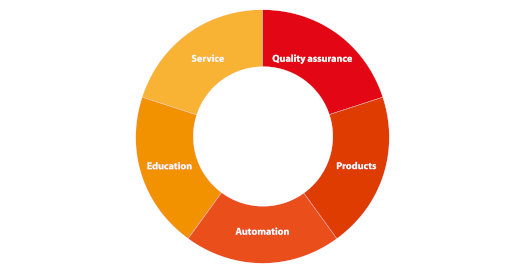