Onze Thije proudly tells...
Revolutionary, enthusiastic and determined is what characterises Elektrolas. And so do our employees.
"The challenge is to always see if something can be done"
"As a technician, you are sometimes quick to say something cannot be done. But if you think about it for a moment, you can find out that it is possible after all." That is exactly where Elektrolas' strength lies. Thije van Delft has been with us for 10 years and recently took charge of the new Cobot Centre. "I always keep my eyes and ears open, looking for new innovations," he says.
"Elektrolas' major strength lies in listening to our customers' needs. Perhaps sometimes we listen a little too well, when we propose a solution we do not even sell ourselves. But I believe that is precisely where our charm lies." Ten years ago, Thije joined us when he was 18-year-old. He started working as a service technician and meanwhile studied mechanical engineering.
In the meantime, things have changed. Thije continued to grow and Elektrolas is increasingly transforming into a service and project organisation. Thije explains how this is reflected in the Cobot Centre: "The great strength of Elektrolas is that we listen to the customer's needs. We have been doing this for years by not only selling our products, but above all giving the right advice with them. In the Cobot Centre, we take this one step further: we first listen to what the need is, and from there we look for the solution that fits best. That could be a cobot, but also a robot or another welding device."
Learning and experimenting
While robots and cobots have been around for many years, Thije sees that companies still do not always know what welding operations they are useful for. He says: "Sometimes customers come to us asking: can you supply device X to us? Many companies would just do that. Elektrolas does not. We start by talking to them to find out why they need this equipment. Then it sometimes turns out that another solution fits the problem much better. Sometimes we propose solutions that aren't directly beneficial to Elektrolas but are important for our customers. I would rather be honest so they really benefit from my advice than sell something that doesn't work as expected."
At the Cobot Centre, companies are welcome to learn and experiment with cobots and robots. Thije and his colleagues also ensure here that all cobots work perfectly before they go to customers. Thije: "In the new premises, we can show exactly what the possibilities of cobots are. We give instructions, build installations and make sure everything works exactly as the customer has in mind. That way, there are no surprises. Once the cobot is finished, we transport it to the customer's site, do a test weld and give the welders training. Within an hour and a half, they can be up and running. It could not be easier."
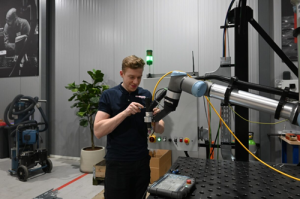
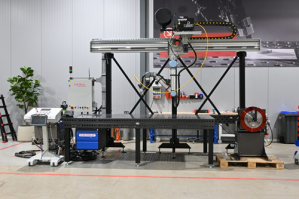
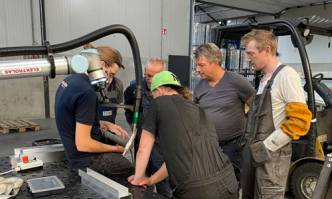
Self made products
Elektrolas has been dreaming of developing its own products for 20 years. That dream is now on the verge of coming true. Thije: "For our cobots, we buy many parts from other companies. But too often those parts do not work exactly as we want them to. Then the question is: are you going to improve what is not completely right, or are you going to make the product yourself so that it fully meets your requirements? This is the latter we are now going to work on."
For example, Elektrolas recently developed its own manipulator. Thije continues: "With the manipulator we bought in, we couldn't do everything our customers asked for. We adapt our own disk exactly to the customer's wishes. This allows us to go much further. Other components, such as the track over which the cobot can move, also performed inadequately in our eyes. Our own version works better and is more flexible to adapt to end-user demand. I look forward to making a lot more products myself."
Hey robot…
One development that has gained momentum last year is that of artificial intelligence. AI also offers opportunities in the welding world. Thije: "We are now working for a customer on a cobot that scans a frame by itself and then calculates what the next step should be to weld the frame. That's a great application, but a lot more is possible. I can just imagine that in the future you will not have to program, but can just say what you want. No more 'Hey Google, play music', but 'Hey cobot, weld this product.' We will also keep up with these developments at Elektrolas."
What the future holds, nobody knows. But what we do know is that Elektrolas is ready for it. Thije concludes: "Our welding knowledge and service are in good shape. That gives many customers the confidence to also choose us as their automation partner. And with success, as we have already helped several companies to produce more efficiently."
Would you like to experience working with a cobot yourself? Come along for a demo at our Cobot Centre. Contact Thije at +31 (0)31901356 or thije@elektrolas.com to make an appointment.